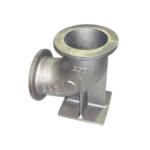
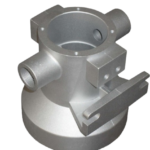
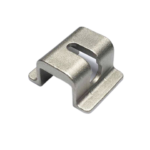
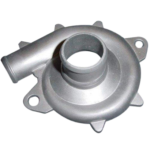

Previous
Next
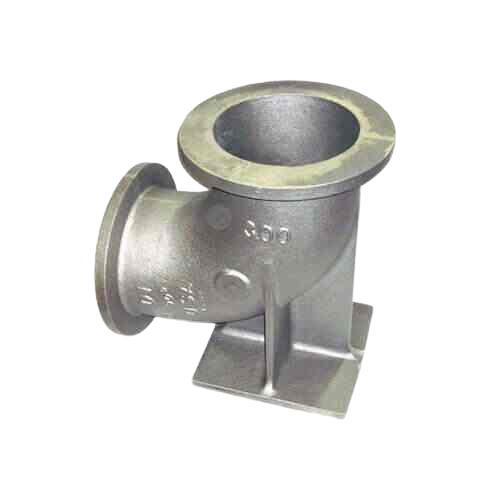
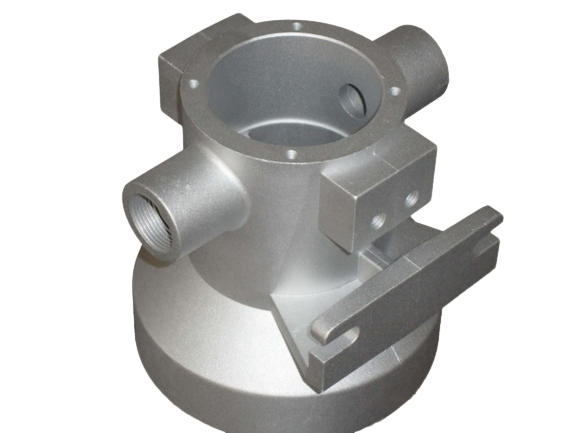
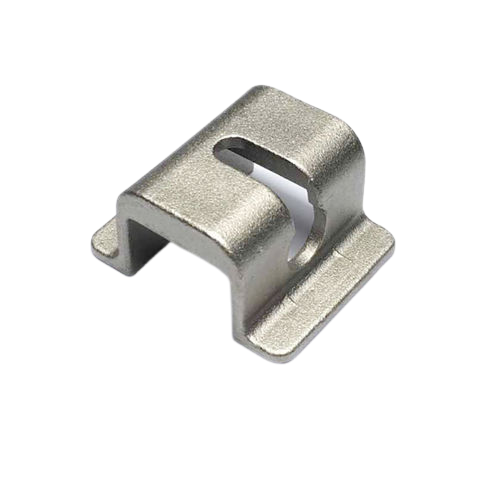
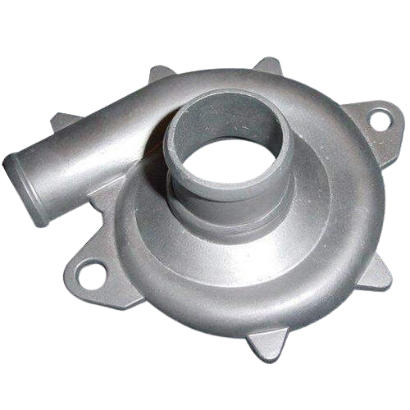
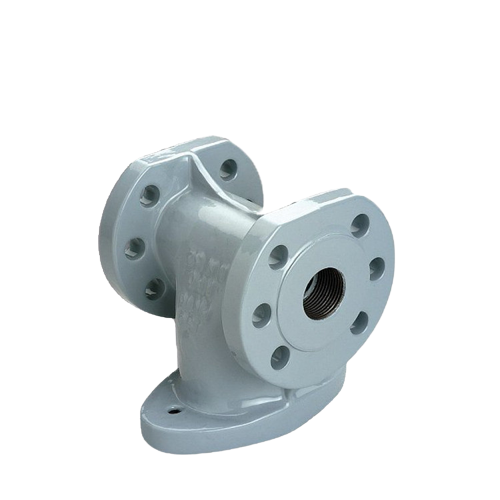
Process:
01
Sand Preparation
Prepare sand and core sand for molding, generally using a sand mixer to mix the used sand and the right amount of clay.
02
Pattern Making
Molds and core boxes are made according to the part drawings. Generally, we can use wooden molds for single parts production, plastic or metal molds for mass production, and pattern plates for large castings. Nowadays, molds are made by engraving machines, so the production cycle is shortened significantly, and it could take 2 to 10 days for mold making.
03
Molding
Molding includes sand molding, core making, and mold fitting. Sand molding means forming the cavity for the casting from the molding sand. Core making refers to the production of the cores, which are used to form the internal shape of the casting. Mold fitting is the assembly of the upper and lower sandboxes after the cores have been placed inside the cavity. Molding is a crucial part of the casting process.
04
Melting
The chemical composition needs to match the required metal. A suitable furnace is selected to melt the alloy material to form a qualified liquid metal (piece and temperature of the molten metal must comply). Melting adopts cupolas or electric furnaces (due to environmental requirements, cupolas have mainly got outlawed, so electric furnaces are the primary choice).
05
Molten Metal Pouring
The molten metal from the electric furnace is poured into the mold using a ladle. The speed of pouring is critical to ensure that the molten iron fills the entire cavity. It is also dangerous to pour the iron, so be careful!
06
Sand Removal
After the molten metal solidifies, take a hammer to remove the sprue and shake off the sand from the castings. The castings are then blasted with a sandblaster to give a clean surface!
The casting blanks are ready to leave the factory after inspection.
07
Grinding
For castings with special requirements, or where the surface of the casting blanks cannot be up to expectation, simple grinding is necessary. And grinding is usually done with a grinding wheel or grinder to remove burrs and give the casting a better finish.
Process Capabilities:
Part Range: 1Kg To 450Kg
Materials availability: Alloy Steel, Carbon Steel, Cast Iron.
Surface Finish: 3.2Ra Onwards
Tolerance: ±0.5MM
Advantages:
Can produce very large parts
Can form complex shapes
Many materials option
Low tooling and equipment cost
Short lead time possible
If you need more info please contact us!